Every site we work on comes with its own unique challenges, and our team is known for its ability to adapt and overcome. We are connoisseurs of the fine art of “whatever the heck it takes to get the job done right.” This particular site near Ely, NV, however, required some pretty spectacular creativity and perseverance, and I felt that it made for a fantastic story about what it actually takes to build great infrastructure.
When a customer asked us to build a simple 200’ tower, Pat O’Laughlin, Director of Construction at our Las Vegas office, said what we always say: “Of course! We’ve got crews that know exactly how to do that.” Then, he found out *where* they wanted to build the site. To improve rural access, our customer needed to build this cell tower on a remote mountaintop near the Nevada / Utah border, above the treeline at 8,500’ elevation, and 40 miles from the nearest town. Only a very rough, narrow dirt track allowed access to the site and local regulations kept the team from improving that road to allow larger vehicles to drive it easily. Pat had just been presented with a doozy of a logistical problem. Other firms had looked at the site and declined the job because of the challenges, but Pat’s and the rest of the Las Vegas team have a lot of grit and “stick-tuitiveness,” and they wanted to go above and beyond for their customer. So, they said yes, and the team started getting creative.
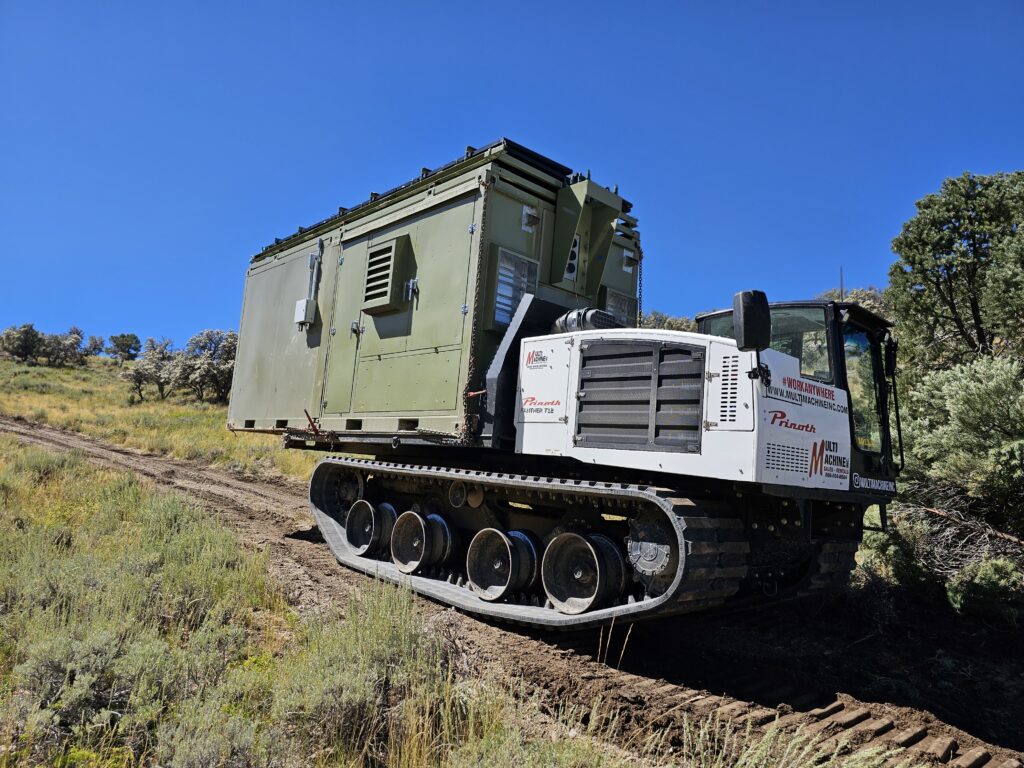
Their first challenge was laying the foundation. Because of the tower’s location above the treeline, it would often be subject to strong winds. That required a sturdier tower, with deeper anchors, and therefore a larger foundation. So, they needed a lot of concrete. But there was a big problem: the cement trucks could not make it from the concrete batching plant in Ely, up that steep road to the top of the mountain. Pat even explored an option using a helicopter to fly the concrete up, but the local helicopter service got pulled into wildfire firefighting duty. Finally, he came up with the genius idea to have bulldozers tow the batching trucks up the mountain and then having them batch the concrete at the site. It wasn’t the simplest option to pull off, but it got the job done!
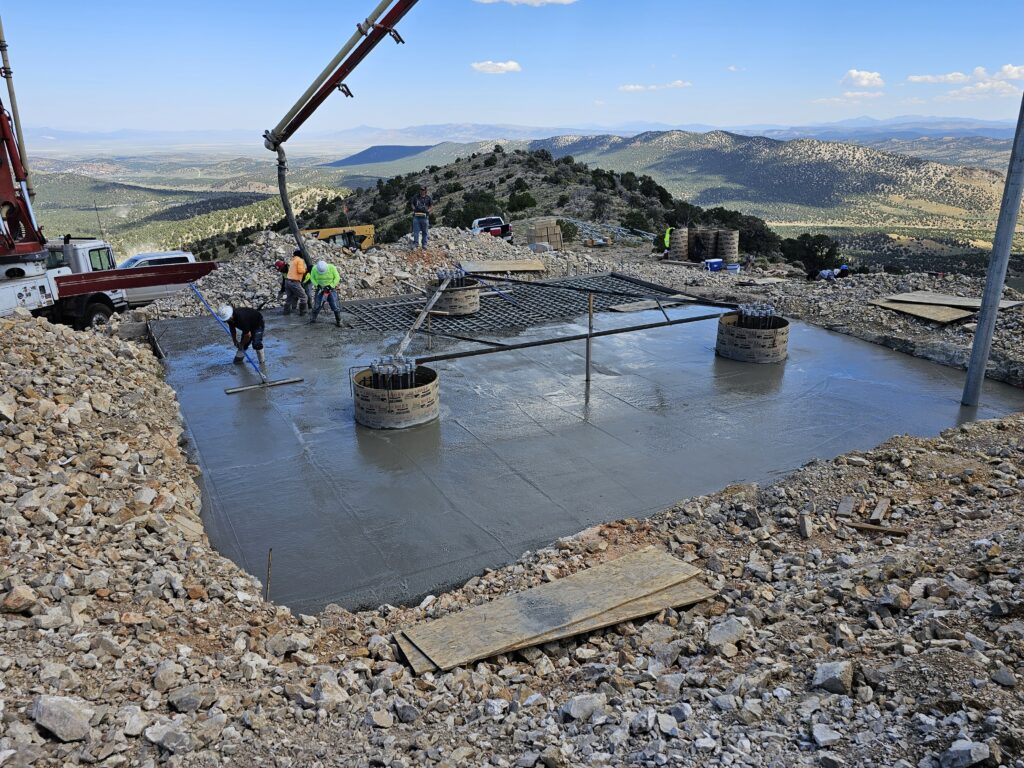
The next challenge Pat and his team had to contend with was the mountain weather. Halfway through batching and pouring the foundation, there was an unexpected torrential downpour. They had to stop working, because even with the bulldozers’ help, the trucks couldn’t make it up that track in the rain. However, before concrete hardens, rain can cause what is called a “cold joint,” or a structural abnormality. Pat and his team are never OK with sub-par work and thought they might have to start all over again. However, luckily, the engineers who designed the site had accounted for at least one rainstorm in their concrete mix specifications, so, after the rain stopped, the team was able to get back to work and know that that their foundation would be fine and sturdy.
Every aspect of this job provided a puzzle to solve – even transporting rebar up the hill. The foundation design required 260 pieces of rebar, each of which was 40’ long, 1 1/8” wide, and weighed 200 lbs. When you start thinking about loading a 40’ long piece of rebar onto a standard vehicle, it gets complicated quickly, between the weight, the sharp bends in the track, and the steep angle of the hillside. Typically, you’d put them on a trailer, but there was no way a trailer was going to make it up that road. So, once again, Pat got creative. He knew he could get a bulldozer up the track, and that a bulldozer was rated to carry the weight of a rebar bundle, so he lashed the bundles to the blade of the bulldozer in the front and to the winch in the back, and, going slowly and carefully to avoid trees, got all 260 pieces of rebar up the mountain.
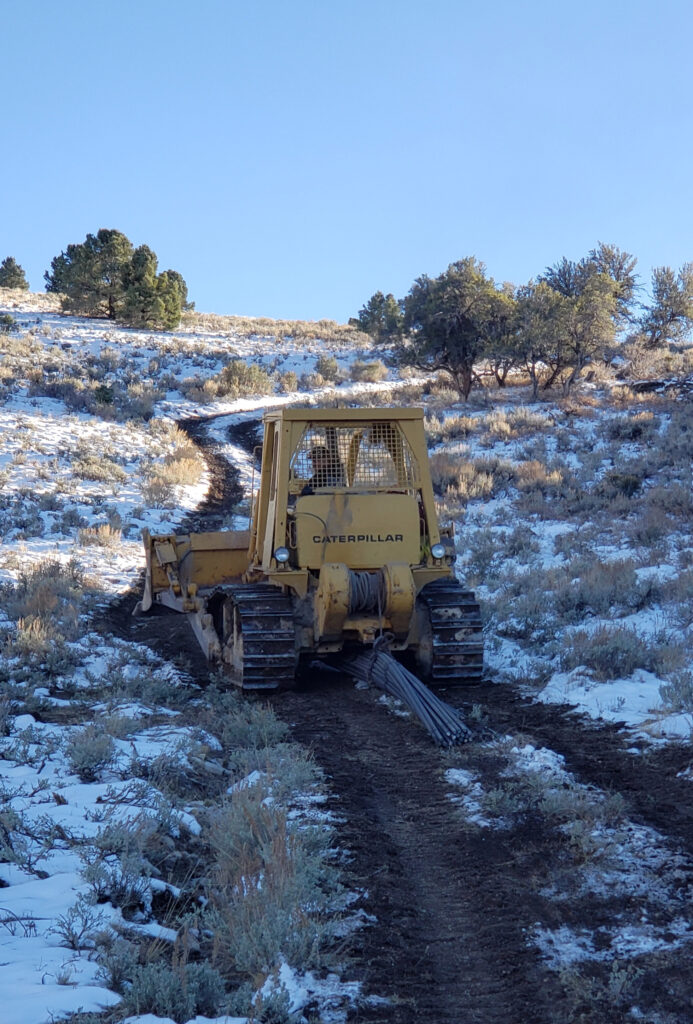
To withstand the winds above the treeline, the cell tower itself had to be pretty massive. Some of the bottom sections were 18” in diameter, 20’ long, and weighed 6,300 lbs. All the tower sections had to be assembled on top of the mountain, because they were too big to bring up assembled. Even the cross-pieces weighed 600 lbs. apiece. If you can imagine the team using a forklift and lifting straps to maneuver each piece into place, in high winds, with rough terrain and dust, you’ll start to get a sense of the huge effort that went into building this tower.
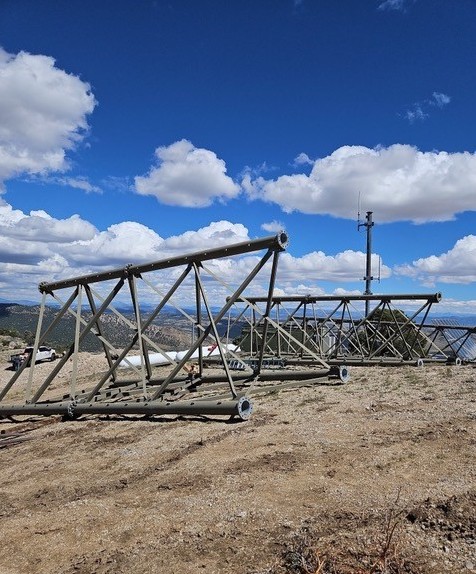
The team also had to figure out how to get power and signal to this totally off-the-grid location. The local utilities were not able to run electrical lines or fiber to this site. And no matter how sturdy a tower is, it’s no good to anyone if it can’t power antennas to improve the network. This is where NextEdge’s experience in Clean Energy came in handy. The team was able to design and build a solar array and a wind turbine, with a battery storage system, to supply sufficient power to the site, with a diesel generator as a backup. We also built a microwave shot to another site with a fiber backbone for signal.
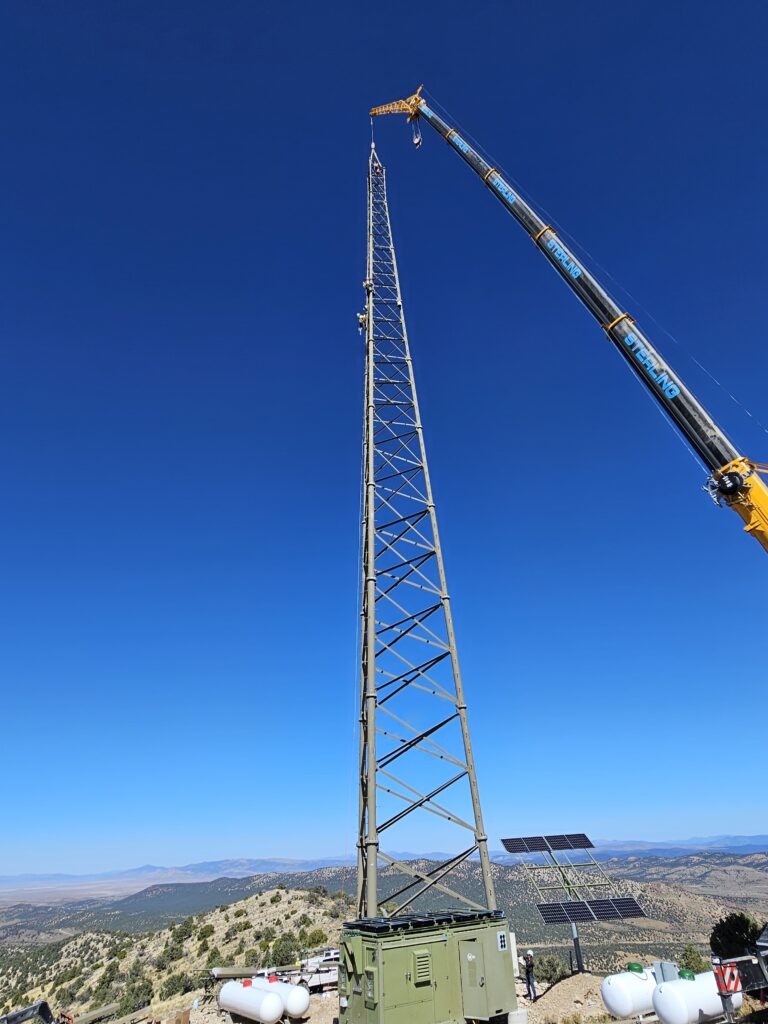
Last but not least, since there was no cell signal for miles around the site until the tower was built, the team’s resource planning had to be 100% on point. If they forgot a tool or a particular bolt, they could not call someone to bring it from the local hardware store. They would have had to stop work and drive 40 miles each way to get what they needed. It was critical that, when they left the shop, their project management team made sure they had everything they needed to get the work done. Luckily, NextEdge has some of the best Project Managers in the business and they were able to stay on track.
In the end, the team built a piece of infrastructure that will stand the test of time. They accomplished a feat they can be immensely proud of and improved cell service for an underserved rural area. Kudos to Pat O’Laughlin and the Las Vegas team for their creativity and perseverance. Keep up the good work!
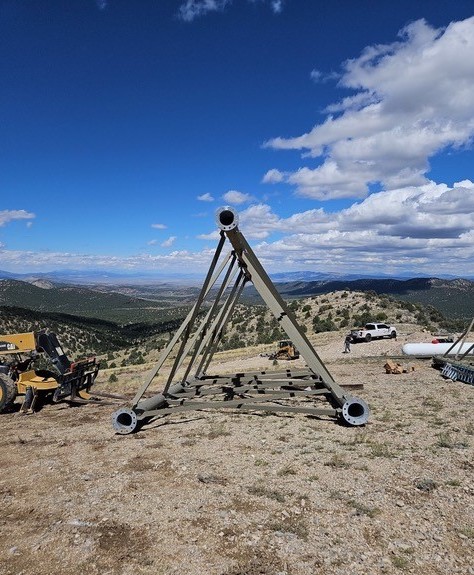
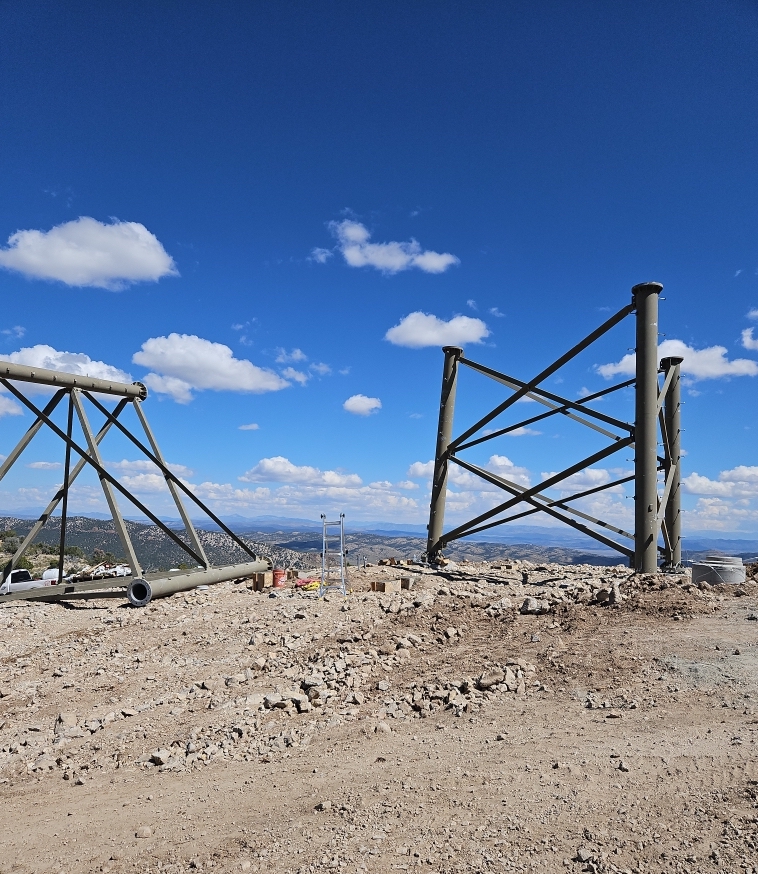
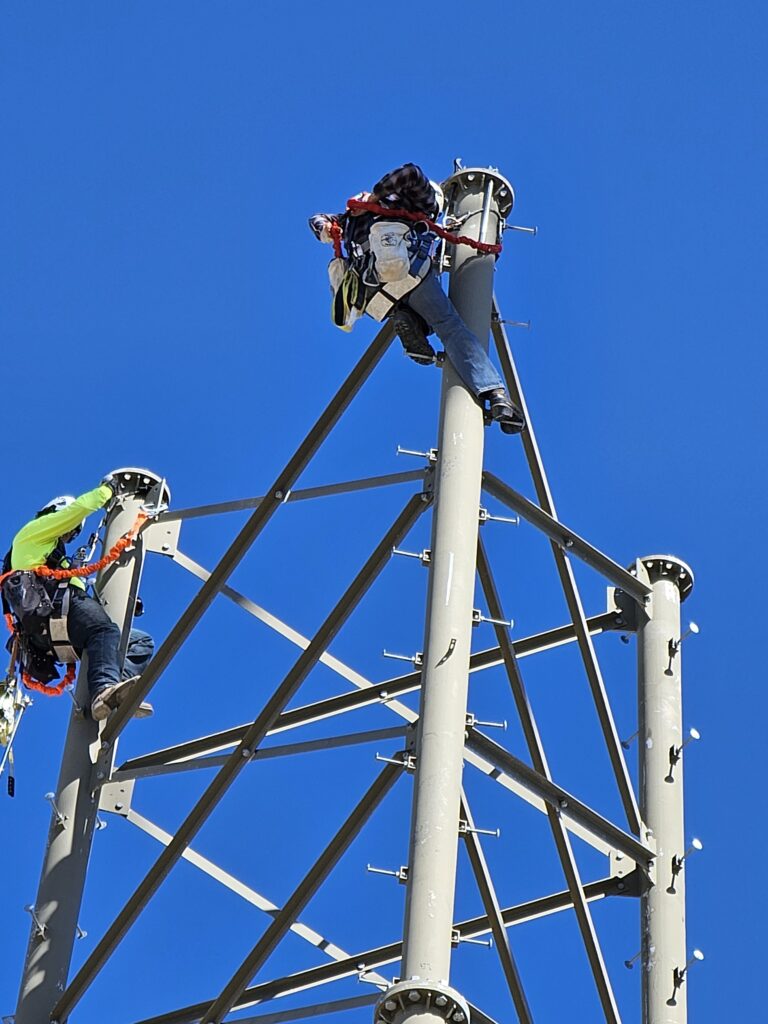
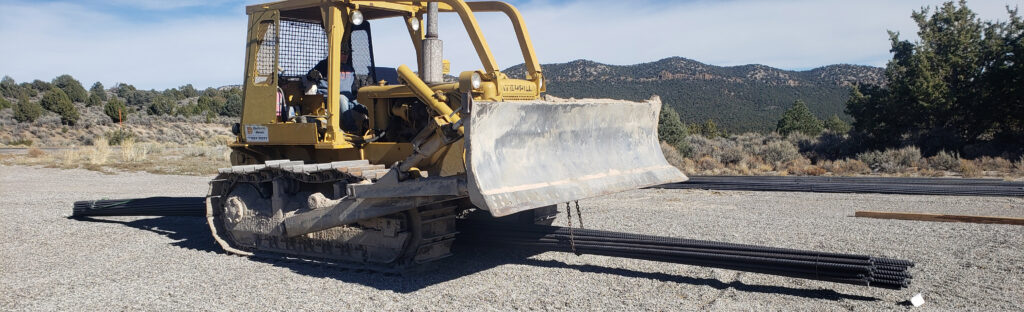